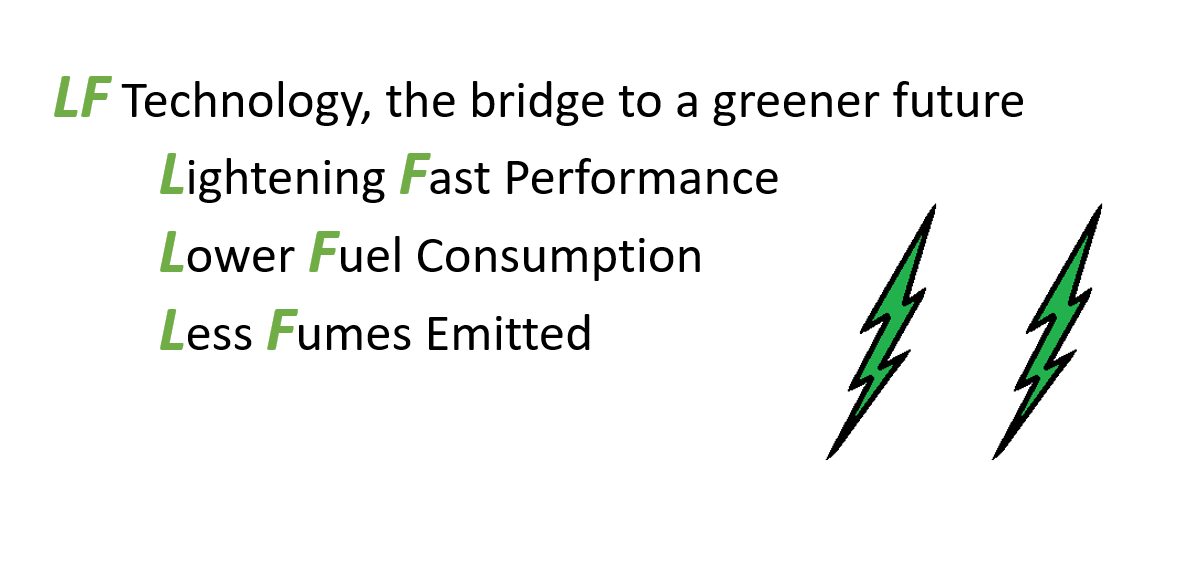
Introducing our Low Friction System
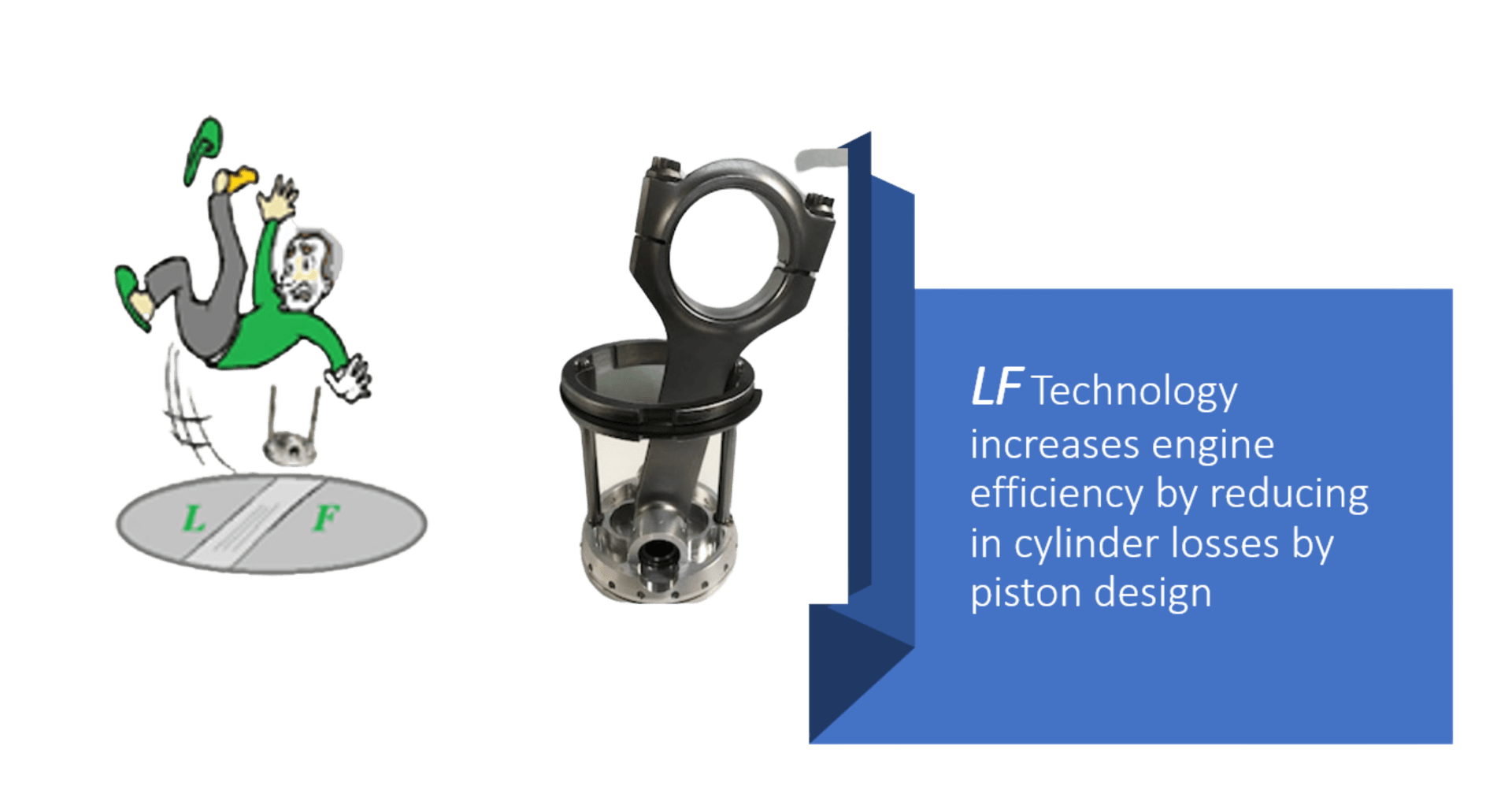
Low Emission Internal Combustion Engines Explained
LF technology is designed to reduce the friction between the piston rings and piston skirt with the cylinder wall. This is done by adding stabilizer bars to keep the piston from trying to turn in the cylinder. Ideally the piston skirt will never touch the cylinder wall and the piston rings will travel smoothly over the honing in the cylinder wall.
Where does an engine lose energy?
We increase engine efficiency to achieve environmental emissions reduction
Introducing Our Low Friction System
Revolutionizing environmental emissions reduction
Our low friction system combines the piston, stabilizer bars, collar and connecting rods to form a low emissions internal combustion engine. By combining these elements into one connected unit, we reduce the friction created in the engine. Because of their adaptable design, the LF system could be a direct replacement for any engine. Likewise, any if could be incorporated in any new engine design coming to market.
Objectives for Low Emission Internal Combustion Engines
INCREASE EFFICIENCY
Increase the efficiency of gasoline engines by at least 15%, from 30% to 45%.
NO COST
INCREASE
Reduce friction of piston rings and piston skirt without increasing cost.
REDUCE CARBON
EMISSIONS
Reduces gasoline consumption and environmental emission reduction by a third
EASY
INSTALLATION
Our design is so simple that anyone can install it with minimal direction.
RETROFIT EXISTING
PISTONS
The new low friction design can replace any existing piston to transform any engine.
REDUCE HEIGHT
AND WEIGHT
We will reduce piston height and weight without increasing cost.
Environmental Emissions Reduction
Making internal combustion engines more efficient
Internal Combustion Engines are known to have low efficiencies. Because only 30% goes to the driveshaft, we should start with the biggest energy losses first. The biggest loss is the friction of the piston rings and piston skirt, followed by the energy required to operate the valve system, closely followed by the pumping losses, and then the water pump, oil pump, crankshaft, etc.
About half of all the friction is in the pistons and rings. If we could reduce that friction by half, we would get a 45%/30%/15%/10% engine.
Addressing Energy Losses while Reducing Environmental Impact
Our low emission internal combustion engine eliminates the "tilting" of the pistons so the skirts never touch the cylinder walls and the rings can't bite into the cylinder wall. We will add stabilizer bars to the piston and eliminate the piston skirt. This will reduce friction while maintaining or reducing the piston weight. This not only increases fuel efficiency, but also has an environmental emissions reduction effect of nearly one-third.
ALL FUEL TYPES
ALL ENGINE TYPES
The beauty of the low emissions internal combustion engine is it can be installed universally. Any engine can be retrofitted with our components to instantly create a low emissions internal combustion engine. All fuel types including gasoline, diesel, two stroke, compressors, and even alternative fuels.
In addition, our system will work with any engine design. We see potential to revolutionize the auto industry, but we won't stop there. Our low friction system can be used in motorcycles, airplanes, farm equipment, lawnmowers and much, much more.
Reduce Friction
Reduce Emissions
Piston Angles
Friction Increases with piston angle. When the skirt touches the cylinder wall, the friction increases dramatically.
Oil Ring Friction
The friction of the oil ring is not shown. It is about two thirds of a compression ring for this piston and ring combination.
RMP Increase
As the rpm of the engine increases the skirts contribute more to the friction as can be seen in the third slide
Lighter Components, Less Waste
Piston Weight Reduction
The lower the piston weight, the less force on the connecting rods and crankshaft. Because force equals one half mass times velocity squared, reducing the weight can allow the engine to run at higher rpms.
Piston Height Reduction
By reducing the height, we can move the collar up in the cylinder and reduce possible stabilizer bar to connecting rod interference. We use shorter pistons to reduce the height of the cylinder and hence, the height of the cylinder block.
Piston Cost Reduction
We work to reduce costs for the customer. One way to accomplish this is by eliminating the cost of the oil rings, one compression ring, and the cost of the machining the piston. Less weight means less cost for most pistons.
PRECISION BALANCE
Designed to maintain the balance of the original engine without rebalancing
When we redesign the engine, the new piston has the added weight of the stabilizer bars. To offset this additional weight, we use titanium wrist pins in place of the original steel wrist pins. This balance must be precise.
The connecting rod is very carefully designed, with extra care given to ensure it is exactly the right size. The stabilizer bar must pass through it, and it must clear the bushing by which the stabilizer bar is retained.
Lowering Cost while Reducing Emissions
The use of all steel pistons will reduce the production cost by one third. In the Ford F150 line, that totals $9 M savings per year. If we extrapolate that to all cars produced in America, it represents significant savings in both dollars and emissions.
Positive Market Outlook for Sustainable Technology
In the US, there is currently a demand for 15 to 17 million new cars per year. With that in mind, there is a need for 75-100 million low friction pistons for cars and trucks alone. The US diesel market is smaller, but due to emissions standards, the need is even greater. When you add in small engines, such as lawn mowers, and large engines for farm equipment, airplanes, etc, there is an expansive US market alone.
We believe our technology is set to revolutionize the green energy movement. As the most polluted cities in the world are faced with ever tightening emissions standards, we offer a low cost effective way to reduce smog and carbon emissions. If every vehicle in the US used LF Technology, we could reduce the use of oil by 30%, reduce gaseous emissions from vehicles by 30%. Contact us today to get learn more about our patented low emissions internal combustion engine modifications!
Mexico LF Contribution
We partner with Mexico LF to work with existing agencies
Our vision for Mexico LF is to work with the Mexican and Mexico City governments to pass laws that mandate the use of LF technology to reduce emissions. The new laws would be along the lines of the laws already in force in Mexico City. Automobile and truck companies would be given a certain period of time, such as three years, to convert their engines in new vehicles to LF technology. After this time, they must become certified or lose the right to sell vehicles.
Existing vehicles would be given a period of time, such as ten years, to convert to LF technology or lose the right to be licensed. All engine rebuilders would be given a period of time to convert all rebuilding to LF technology.
Building a
Better World
Lowering the friction in piston driven equipment will be required in the next 10-20 years will be crucial. It lowers the dependence on foreign oil, reduces emissions, runs cooler, lasts longer, and costs less than existing technology.
Frequently Asked Questions
Have a question? Please contact us today.
Let’s Talk
Do you want to learn more about low internal combustion engines but don't know where to begin? We're here to help you get started.
Don't wait another moment. The time is now. We can't wait to partner with you on your journey to sustainability.